Run Execution
Factory OS
Case Study
B2B SAAS
Sr. Product Designer
Read Time: About 5 minutes
Open Index
Transforming Technician Workflows in Agile Manufacturing
The redesign of Run Execution (Run.exe) within ION Factory OS, a manufacturing 4.0 software solution, aimed to enhance productivity, customer satisfaction, and operational efficiency for agile manufacturers (learn more at FirstResonance.io). Run Execution, the most-used section of the platform, delivers work instructions segmented into steps for technicians to execute complex hardware assembly tasks. However, the legacy interface had significant issues, some adding countless hours due to unnecessarily repetitive tasks.
As the acting head of design at First Resonance, I led the complete redesign process alongside my team, focusing on creating an intuitive, scalable, and responsive solution. We aimed to simplify workflows, streamline user experience, introduce enhanced functionality, and improve the platform's performance.
Actual footage using the beta Run Execution and the legacy Run Execution rendered in real time for the 2024 roadmap video. Watch the entire video here.
Current Challenges
Technicians using the original Run.exe faced several challenges:
Slow Interface:
The legacy system would run into frequent slowdowns, adding unnecessary time and cost to assemblies.
Hidden Primary Actions:
Unnecessary features cluttered primary technician tasks, reducing focus and increasing time on task.
Lack of Responsiveness:
The interface needed more optimization for many customers' primary and secondary devices.
Inefficient Team Sign-in and Sign-off Process:
Most customers built larger hardware with teams and required sign-offs when completing steps. Users would sign in with a separate browser, incognito window, or device.

Legacy Run Execution
Design Goals
Our design team set out to address these issues by focusing on the following:
Improved Technician Workflows:
Streamline task completion by making key actions accessible and less ambiguous.
- Enhanced Visibility and Signaling: Increase the visibility of the "clear to build" signaling and indicate all blockers in the Run.
- Optimize Load Times: Bring lazy loading to work instructions and data grids.
- Improve Traceability: Give contextual information where necessary to increase transparency and traceability of tasks and objects.
- Improve Data Collection: By introducing keyboard shortcuts, users can use just the keyboard for laborious tasks like data collection and multiple-part installations.
Optimized Workflow for Engineers:
Enhance and provide additional tools and controls for engineers but keep them secondary to technician needs.
Device-agnostic Responsiveness:
Ensure the system adapts to different viewports for technicians and engineers in all environments.

Part of the process was to ensure the OS was fully responsive. This would allow customers who worked in the field to use the appropriate device for their environment.
My Role
As the acting head of the design team,, I led and executed the entire product design process, which included:
- Research and synthesis of user needs
- Requirements gathering
- UX/UI design, user testing, and beta testing
- Design system creation and maintenance
- Continuous post-release iterations based on feedback
I led and worked alongside a small but talented team and collaborated extensively with engineering, product management, customer success, and customers to ensure that the new Run.exe met our customers' needs.
Process
Research & Problem Discovery
We engaged deeply with our customers in highly technical manufacturing sectors, including aerospace, robotics, nuclear fission, and electric watercraft. Through direct conversations and field research, we identified key pain points. Many technicians shared frustration with laborious workflows, slow task sign-offs, the clumsy interface, and lack of signaling.
In addition to the tremendous qualitative research that sheds light on many great insights, over 90% of the employees at First Resonance worked in the manufacturing space. This institutional knowledge allowed the design team to gain insights into problems quickly. While this knowledge did introduce biases, we leveraged the qualitative research to inform our colleagues what we were learning from our customers.
Meeting users on the factory floor helped illuminate new features and better workflows that weren't immediately obvious from office-based research.

We utilized Figjam extensively for all types of flows and processes. These whiteboards would become part of the living documentation that would be updated and commented on synchronously and asynchronously.
Iterative Design & Validation
Given the complexity of Run.exe, we broke down the main screen into five core sections:
- Utility "Andon" Bar: A quick-glance status bar for signaling if a technician is "checked-in" to a step.
- Run Header: Key information for the entire Run and quick access to engineer tools.
- Step Navigation Panel: A streamlined step navigation system complete with "clear to build" signaling.
- Step Header & Work Instructions: Main task controls and instructions.
- Step Tools Panel: Primary tools for installation, data collection, communication, and dependency information.
We designed each section iteratively, conducting sprints to validate designs internally and externally. Feedback loops with customers and engineering were essential in refining these designs before the final handoff.
One of many Figma prototypes used for testing and marketing.
Utility "Andon" Bar
Inspired by the manufacturing andon system, this bar signals a technician's status: whether they have checked into tasks, are running on time, or are behind schedule. It provides real-time feedback and allows technicians to check out all steps individually or simultaneously, drastically improving time-tracking accuracy.
Result:
Drastically improved time tracking for engineers and technicians who are required to work on multiple steps simultaneously.

The Andon Utility bar was designed to be seen from across a room. An engineer could easily spot an issue by looking at the technician's computer screen.
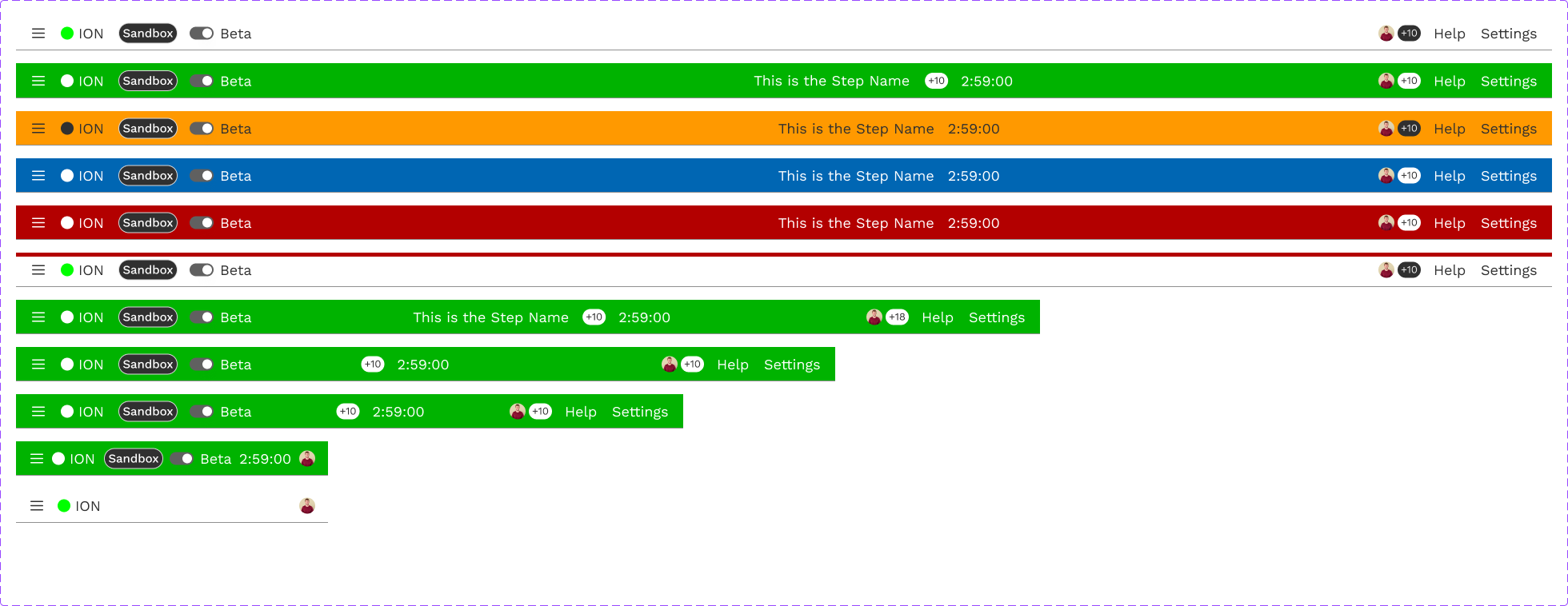
As a part of our signaling philosophy, the Andon utility bar informed and empowered our users. It was also built with machine automation in mind. If a machine or test failed, you could have it turn the Andon red, signaling a failure has occurred.
Run Header
We overhauled the run header to provide concise, crucial information about the Run. Technicians and engineers could quickly see if there were any blockers on the Run, and engineers could quickly access specs, issues, history, redlines, and dependencies, among other tools. We introduced a powerful batch management tool to simplify the management of batched Runs significantly.
Result:
Grouping the engineers' tools and improving workflows for Redlines and Batching reduced engineers' time on tasks from hours to minutes.
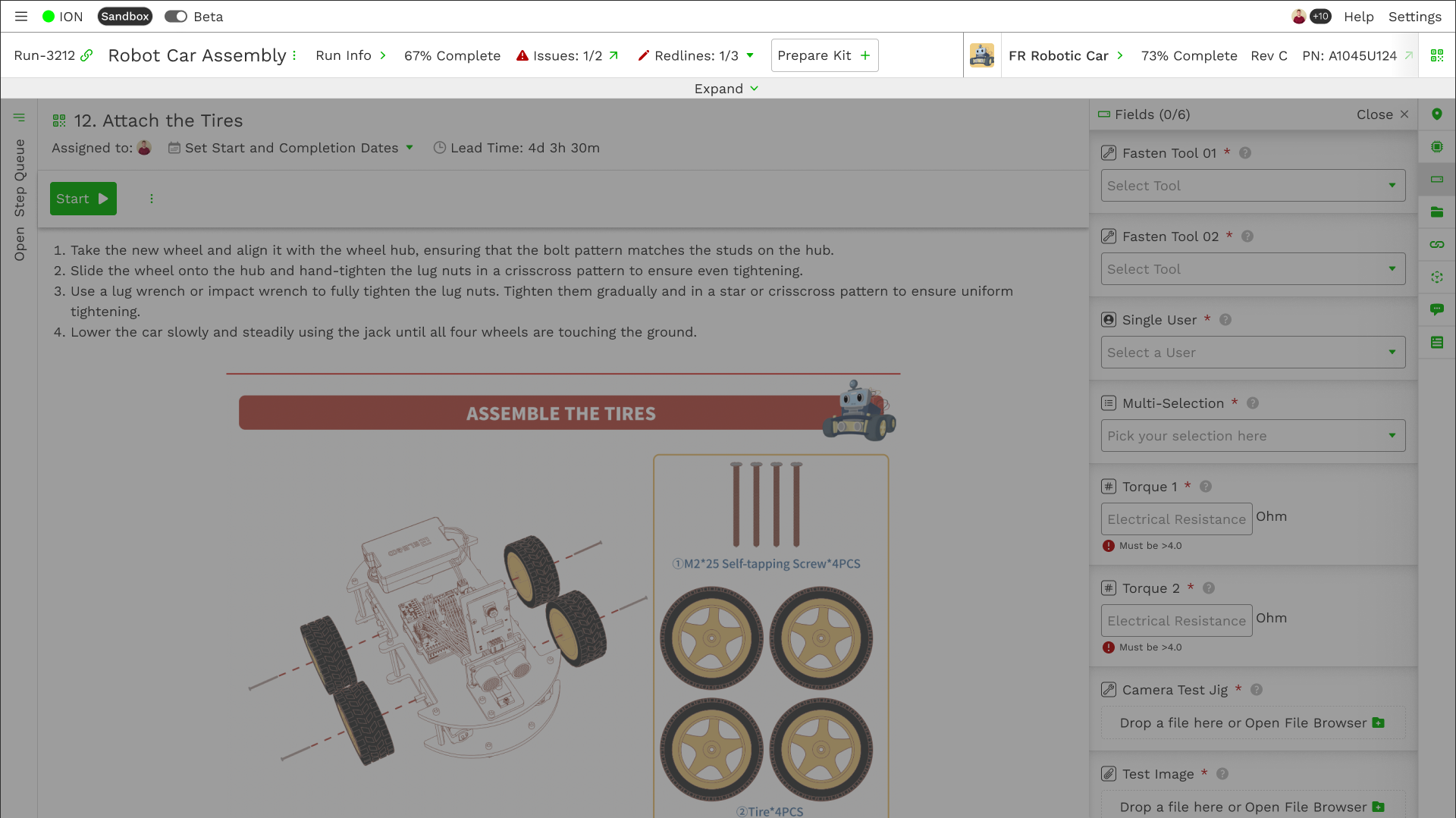
The Run header was responsive. Primary information and signals are always visible.

Secondary and tertiary information and access to tools are accessible with just one click.
Step Navigation Panel
The updated Step Navigation Panel allowed technicians to quickly locate their next task while quickly identifying blocking issues, redlines, and dependencies.
Result:
Faster task discovery, clear signaling, and enhanced technician focus on critical steps.
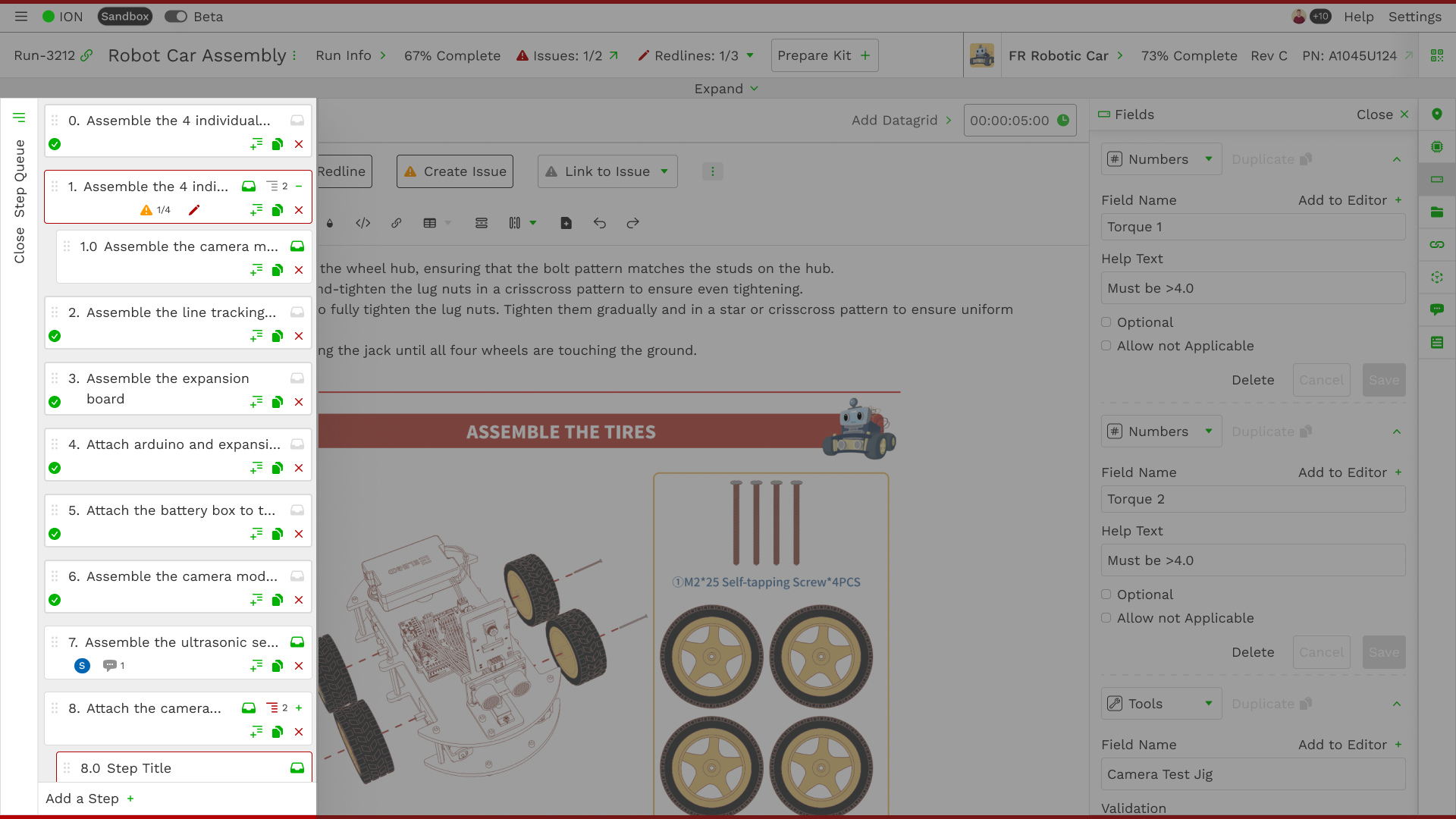
Step Queue signals if a technician is "clear to build." It is also a powerful tool that allows engineers to update the position of each step, copy the step, create a new step, and create child steps.
Responsive Work Instructions
We redesigned the work instructions to be fully responsive, allowing technicians to view tasks across devices with minimal disruption. Additional enhancements included automation for repetitive tasks and a QR code feature that enabled quick check-ins via mobile devices. We also redesigned data grids to allow for more required functionality. The engineering team also added lazy loading, significantly reducing step load times.
Result:
By improving load times and adding functionality to data grids, technicians spent less time navigating steps and instructions.
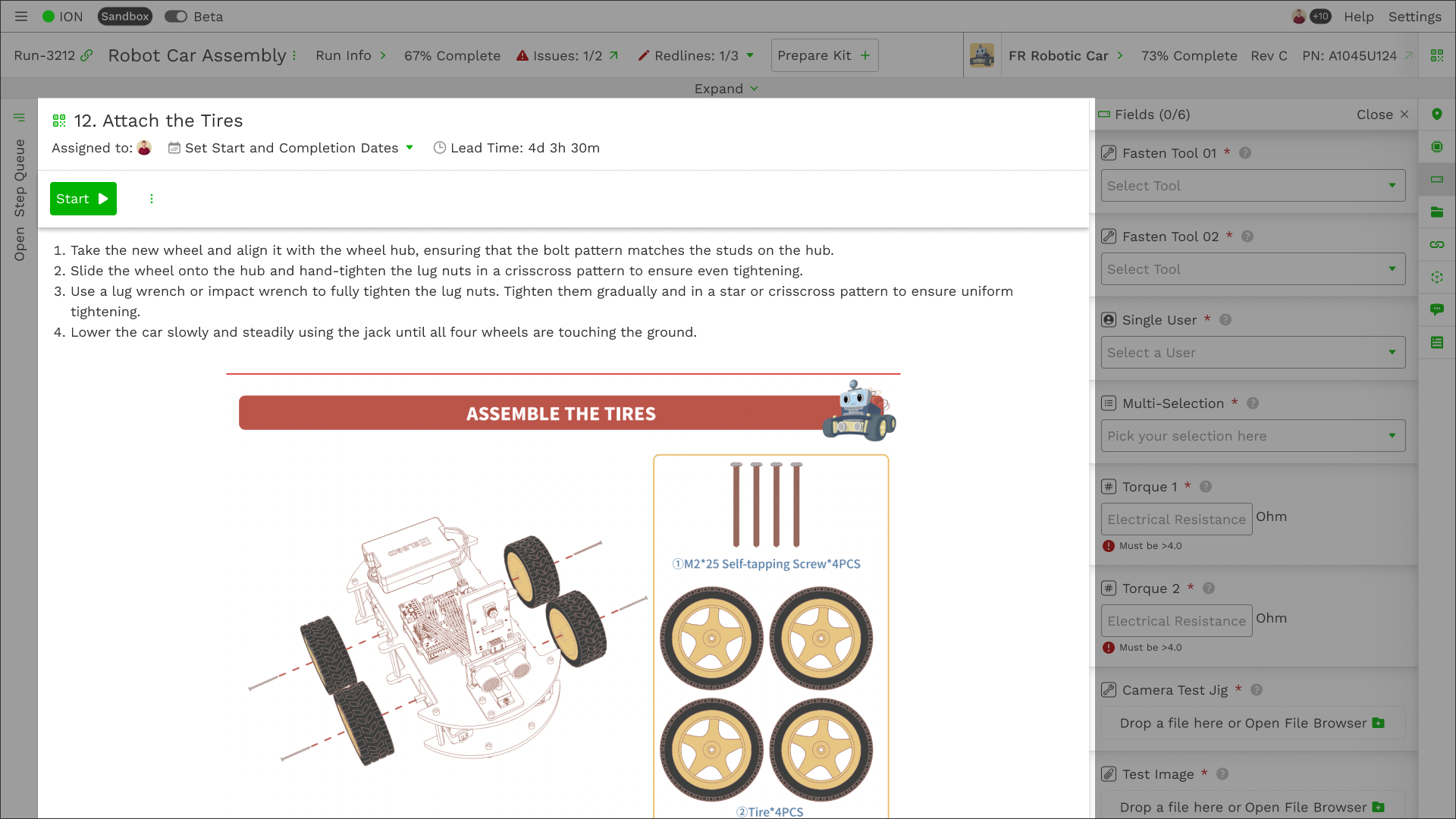
The step header and "check-in" functions were streamlined. The action bar, currently showing the "start" button and sub-menu, would change to show the actions the user would possibly need in their current scenario.
Step Tools Panel
The Step Tools Panel provided technicians with all tools required for secondary and tertiary actions, such as data collection, part installation, and feedback submission. We introduced modals, "called managers," to handle large data sets, making tracking dependencies, installing parts, accessing files, and communicating in complex assemblies easier. We also introduced keyboard shortcuts. The user could easily tab between sections and navigate between and inside fields.
Result:
Time saved per technician and greater flexibility in managing intricate workflows.
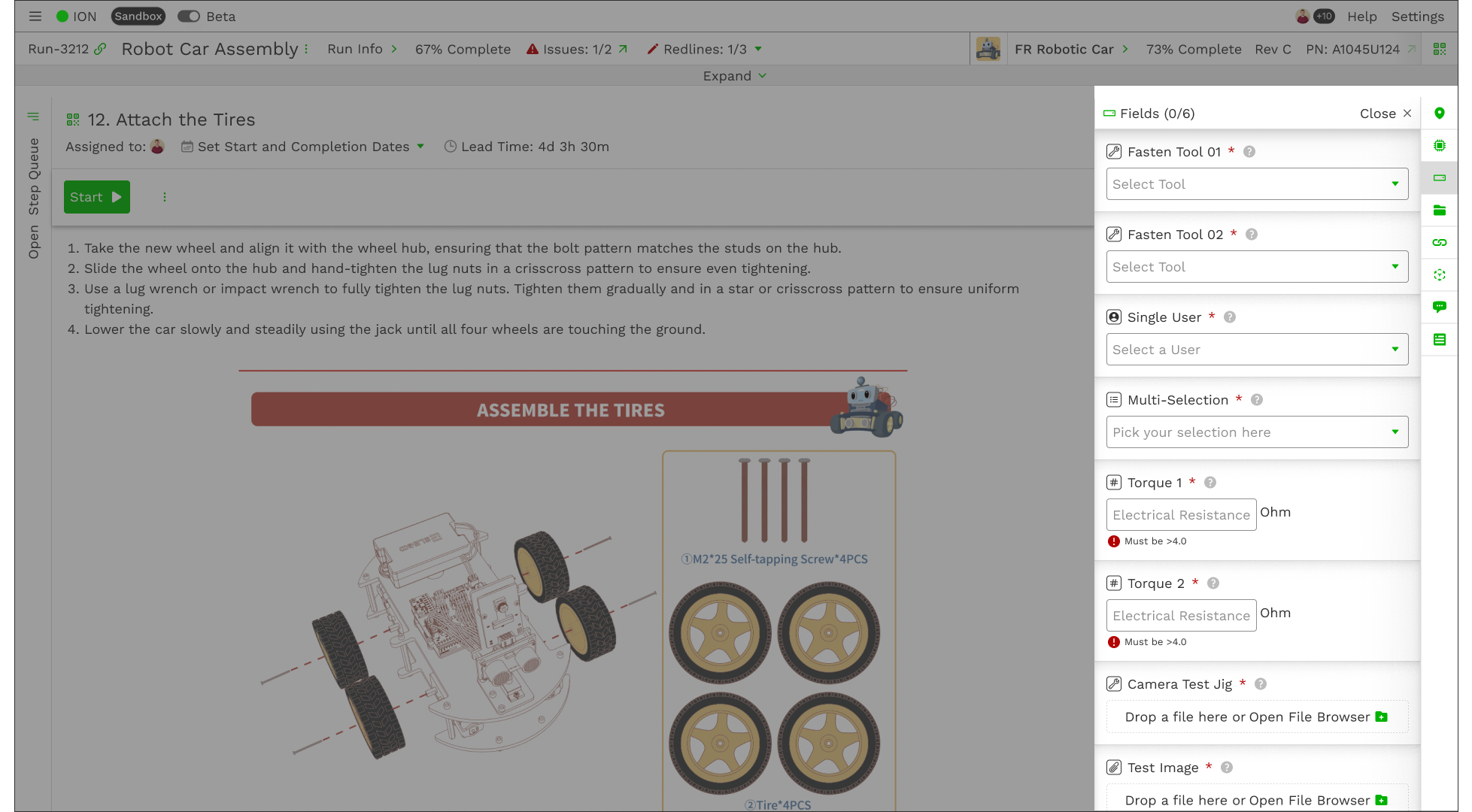
The right rail drawer system allows technicians and engineers to access and input various types of data and communications.
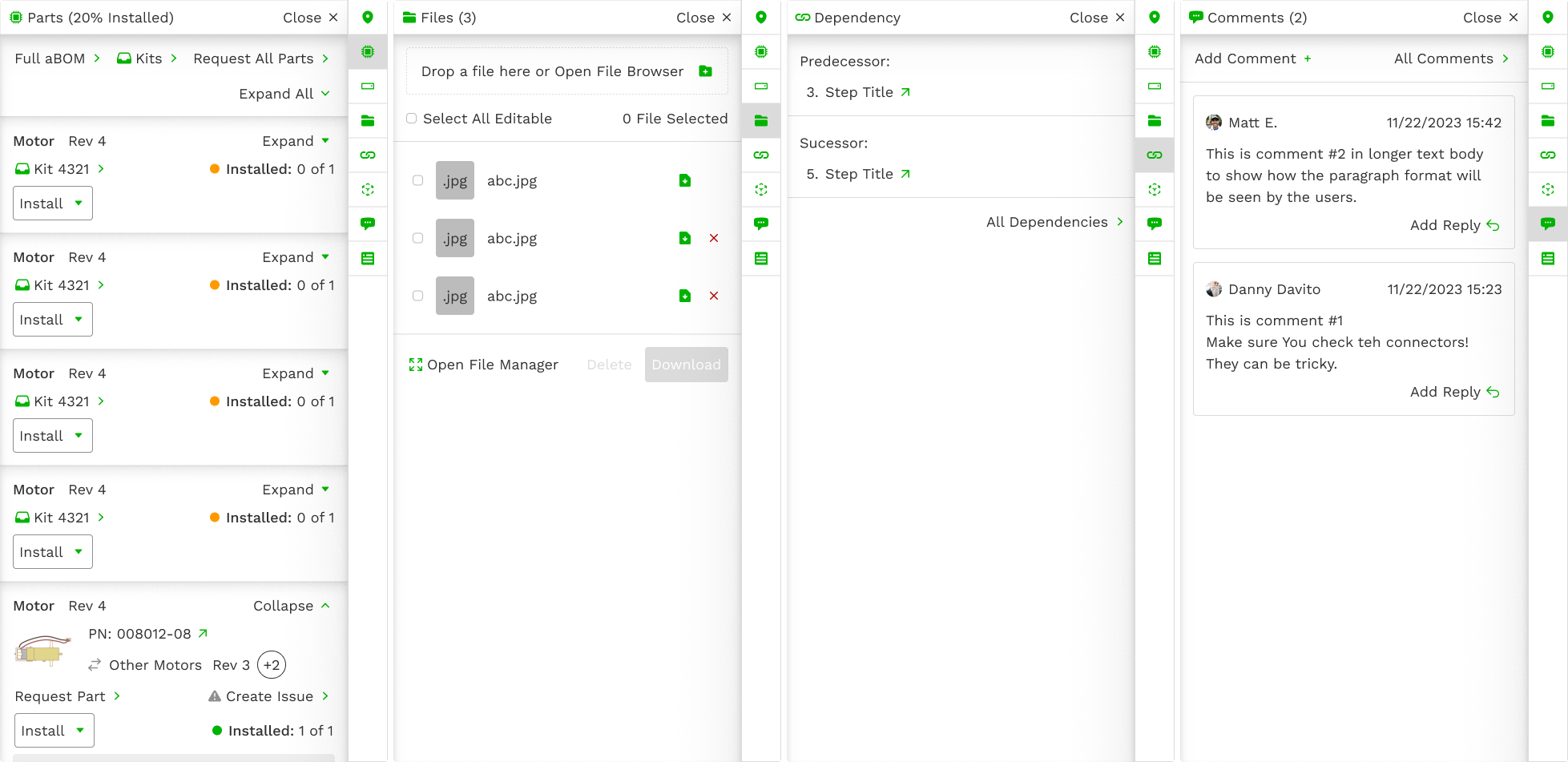
From left to right: 1. Parts to be installed 2. File Manager 3. Dependencies 4. Comments
Impact & Results
Financial Value
- Increased Efficiency: By reducing task completion time and screen load times, we saw a significant increase in technician productivity, leading to cost savings. Some customers experienced a 15% reduction in time on task, while others experienced up to 25%.
- Accurate Time Tracking: Check-out automation increased time-tracking accuracy while technician check-outs increased, enabling a 30% increase in precise cost analysis for each Step and Run.
Customer Value
- Enhanced User Experience: The new UI delivered a seamless experience, focusing on the technician and more intuitive controls, resulting in higher satisfaction among technicians and engineers.
- Bespoke Workflow Flexibility: Device-agnostic access and features like QR code check-ins allowed adaptable workflows across diverse manufacturing environments.
Operational Efficiency
- Streamlined Workflows: The redesign boosted coordination among technicians and engineers, improving workflow efficiency and minimizing bottlenecks.
- Visibility & Traceability: Enhanced task visibility allowed for better monitoring and troubleshooting during assemblies.
Innovation & Growth
- Scalability: The modular design set the foundation for future sections, such as global history and aBOM manager.
- Future-Proofing: New features, including global signaling, batch anything, redline merging, and the dependency and overview manager, further set ION apart from the competition.
By reducing time on task, streamlining workflows, and enhancing functionality where necessary, the new UI significantly increased the ROI of the factory OS for our customers
Conclusion
The redesign of Run.exe in ION Factory OS transformed technician workflows by simplifying the interface, improving task clarity, and enhancing system responsiveness. The result was a more efficient, flexible, and scalable platform that significantly increased user satisfaction and business value.
This project exemplifies how design can impact productivity, satisfaction, and growth in manufacturing, creating a solid foundation for future enhancements.